Формование арамидных волокон на прядильных машинах ПН-300-В2М представляет
собой сложный технологический процесс, в котором сушка нити на сушильном
цилиндре (далее “цилиндр”) является одной из важных стадий [1]. Это связано с
необходимостью удаления избыточной влаги из нитей и проведения предварительной
ориентации макромолекул полимера перед стадией основной термообработки, что
достигается в ходе сушки нити на цилиндре при строго определенной температуре
и натяжении.
Одним из факторов, влияющих на качество нити в процессе сушки на цилиндре
прядильной машины, является качество поверхности цилиндра, которое должно
отвечать следующим требованиям.
1. Поверхность должна быть химически стойкой к агрессивным
растворам-электролитам. Это связано с тем, что параарамидная нить после второй
отмывки несет на себе слабокислый раствор воды с pH = 4 и менее. В зоне касания
нити и цилиндра (особенно на первом витке) происходит постепенное
коррозионно-механическое и водородное изнашивание металла в виде кольцевых
канавок на шлифованной поверхности.
2. Поверхность должна обладать повышенной твердостью и износостойкостью, так как для снятия с
цилиндра подмотов, образующихся при обрывах нити, операторы используют особо
острые ножи, оставляющие на недостаточно твердой поверхности глубокие царапины.
3. Поверхность должна иметь шероховатость не ниже 9-го класса
Rа 0.2-0.1 мкм).
Невыполнение указанных требований приводит к “травмированию” нити при её
перемещении по цилиндру и, соответственно, снижению её прочностных
характеристик.
На предприятии ОАО “Каменскволокно” в настоящее время более 50% цилиндров
требуют замены или восстановления. Одним из путей срочного решения этой проблемы
и экономии материально-сырьевых и энергетических ресурсов является разработка
технологии восстановления цилиндров путем нанесения износостойких и
коррозионностойких неорганических покрытий. Затраты на восстановление в 10-15
раз меньше, чем затраты на изготовление новых цилиндров.
Анализ методов нанесения неорганических покрытий, гарантирующих выполнение всех
требований качества поверхности цилиндров при сушке арамидных нитей, показал
перспективность нанесения на цилиндры покрытий методом детонационно-газового
напыления.
Этот метод позволяет получать высококачественные, практически беспористые
покрытия из сплавов, оксидов металлов, из механических смесей плакированных и
композиционных порошков с высоким уровнем адгезии с материалом основы.
Применение различных порошков дает возможность получать коррозионностойкие,
антифрикционные покрытия. Одним из преимуществ детонационно-газового напыления
является умеренный нагрев покрываемой поверхности изделия (не выше 250°С), не
приводящий к изменению свойств основного металла [2].
Основными технологическими параметрами, определяющими качество и характеристики
покрытий, являются химический состав порошка, состав детонирующей газовой
смеси, средний размер гранул напыляемого порошка и его расположение в стволе в
момент инициирования детонации, дистанция напыления, навеска порошка на один
выстрел, режим подготовки поверхности основного металла, геометрические
характеристики ствола детонационно-газовой установки. При оптимизации этих
параметров под качеством покрытия обычно подразумевают их пористость и толщину
в результате единичного выстрела, а также прочность сцепления с изделием.
Для нанесения покрытия на цилиндры использовалась детонационно-газовая
установка с характеристиками, указанными в таблице.
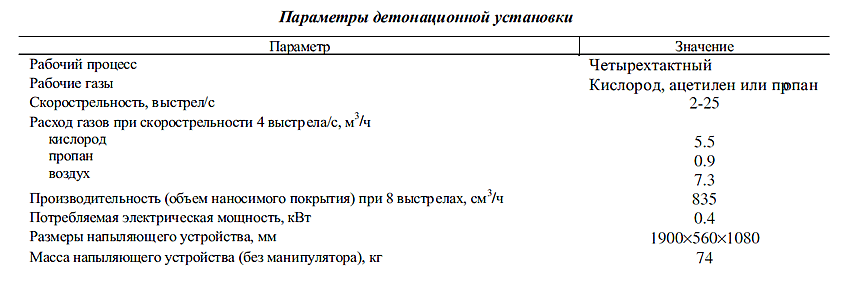
Для покрытия цилиндров использовался порошок самофлюсующего сплава ПР-НХ17СР4
(Ni - 79%, Cr - 15%, Si - 3%, B - 2.4%). Бор и кремний, образующие легкоплавкие
флюсы, снижают температуру оплавления порошков и повышают жидкотекучесть
расплава, а наличие в составе твердых боридов хрома и карбоборидов обеспечивает
высокую твердость и износостойкость покрытия.
Процесс нанесения покрытия состоял из следующих основных операций: подготовка
напыляемых порошков; подготовка цилиндра к нанесению покрытия; нанесение
покрытия; механическая обработка покрытия.
Подготовка напыляемых порошков заключалась в их сушке в печи СНОЛ 3.5 при
температуре 100-120°С в течение 3 ч. Толщина слоя на противне не превышала 30
мм. После сушки порошок охлаждался в печи до комнатной температуры и загружался
в блок подачи порошка в установке.
Подготовка цилиндра к нанесению покрытия заключалась в проточке и шлифовании
цилиндра на токарном станке с удлиненной станиной мод. 3М161 до диаметра 183.9±150 мкм, шероховатостью Ra 6.3-3.2 и обработке поверхности ацетоном перед
нанесением покрытия.
Нанесение покрытия осуществлялось при следующих параметрах
Частота вращения манипулятора, об/мин |
3 |
Количество выстрелов в секунду |
8 |
Объем наносимого покрытия, см3/ч |
835 |
Толщина покрытия, мкм |
600-650 |
На рис.1 показан вид покрытия на цилиндре после нанесения, до механической
обработки. Механическая обработка покрытия осуществлялась на круглошлифовальном
станке с удлиненной станиной мод. 3М172 (3М 151.3) до окончательного размера 185
мм±100 мкм и придания шероховатости Rа 0.2-0.1 мкм. Твердость покрытия после
механической обработки, измеренная по методу Роквелла (HRC), составляла 51-52.
На рис.2 показан вид поверхности цилиндра до и после нанесения покрытия.
Для проведения промышленных испытаний цилиндр с экспериментальным покрытием был
установлен на прядильной машине ОАО “Каменскволокно” в мае 2006 г. Цилиндр
работает до настоящего времени (продолжительность эксплуатации на 01.09.2008 г.
составила 30 месяцев).
После работы цилиндра в течение 2-3 месяцев на поверхности касания первого витка
нити появляется слой накипи, легко снимаемый в процессе чистки цилиндра.
Аналогичное явление наблюдается и на цилиндрах с покрытием из нержавеющих
сталей и Al2O3. На поверхности цилиндра отсутствуют видимые следы коррозионномеханического и водородного изнашивания.
В случае снятия операторами намотов нити на поверхности цилиндра отсутствуют
глубокие царапины, подобные царапинам, появляющимся на цилиндрах из нержавеющих
сталей. Вероятно, это связано со сравнительно высокой твердостью нанесенного
покрытия.
Опытно-промышленный образец цилиндра с разработанным в НПО “Орион ВДМ”
покрытием, нанесенным методом детонационного напыления, рекомендован для
промышленного внедрения на прядильных машинах
ОАО “Каменскволокно” и других предприятий отрасли химических волокон.
- Показана возможность использования детонационно-газового напыления порошков самофлюсующего сплава ПР-НХ17СР4 (Ni-79%, Cr - 15%, Si 3%, B - 2.4%) для
восстановления сушильных цилиндров прядильных машин.
- Приведены результаты эксплуатационных испытаний сушильных цилиндров с
нанесенным покрытием в ОАО “Каменскволокно”.
|