В большинстве случаев процессы
получения углеродных сорбентов связаны с
удалением части вещества из объема углеродных
блоков, гранул или волокон [1]. При этом происходит
увеличение их пористости и удельной поверхности.
Процесс удаления части углеродсодержащего
вещества в результате его травления реагентами
называется активацией.
Активация может осуществляться газами
(газофазная или физическая активация),
жидкостями (жидкофазная активация) или путем
внедрения реагентов в твердые углеродсодержащие
исходные материалы (такая активация называется
твердофазной или химической).
При газофазной и жидкофазной
активации травлению подвергаются материалы с
предварительно сформированным благодаря
термообработке (карбонизации) углеродным
скелетом. Исходное содержание углерода в таких
прекурсорах обычно составляет 80-90%.
При осуществлении твердофазной
активации в качестве прекурсоров могут
выступать как карбонизованные материалы, так и
углеродсодержащие полимерные вещества,
материалы из пеков, лигнина и др. В случае
использования полимеров, пеков или лигнина
процессы активации совмещены с процессами
карбонизации и образования углеродного
трехмерно сшитого пористого скелета.
Для получения активированных
углеродных волокон (АУВ) и углеродных
волокнистых материалов (АУВМ) наиболее часто
используются процессы газофазной активации.
Активирующими агентами выступают углекислый
газ, водяной пар, кислород или озон в инертных
газах-носителях, аммиак. На рис.1 представлена
принципиальная схема получения АУВМ с
использованием газофазной активации.
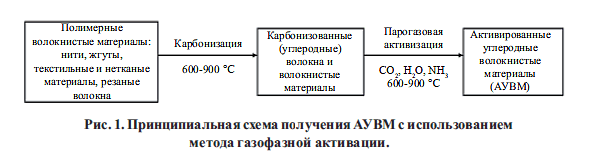
Газофазная активация и способы
получения АУВМ с ее использованием являются
наиболее разработанными и изученными
практически для всех углеродных волокон,
производимых в промышленных масштабах из
полиакрилонитрила, целлюлозы, пеков, фенольных
смол и лигнина [2-9]. Кроме того, начиная с середины
90-х годов прошлого столетия развернулись
исследования по получению АУВ из таких
волокон-прекурсоров, как кевлар [10], номекс [11],
оксалон [12].
Принципиальной особенностью
получения АУВ методом газофазной активации
является использование на стадиях карбонизации
и активации высокотемпературных процессов
(600-950°С), что снижает выход углеродного волокна и
ведет к высоким энергозатратам. Снижение затрат
возможно в случае использования в качестве
активирующих агентов кислорода воздуха или
озона (вместо СО2 и Н2О) и применения
каталитических добавок, позволяющих снижать
температуру активации и регулировать пористую
структуру АУВ [13, 14]. Однако в силу ряда причин эти
технические решения не нашли широкого
промышленного внедрения.
Перспективным как с практической
точки зрения, так и с позиций разработки
теоретических аспектов получения углеродных
сорбентов является изучение процессов
твердофазной активации. Следует отметить, что
метод твердофазной активации известен довольно
давно и применяется в промышленности для
получения углеродных гранулированных сорбентов
[15, 16], однако работ, связанных с получением этим
методом волокнистых сорбентов, крайне мало.
Небольшой раздел, посвященный
химической активации волокон, можно найти в
книге Ермоленко [17], где раскрывается суть метода,
но конкретные параметры процесса и/или
характеристики полученных АУВ, не приводятся.
Идея метода основана на том, что ряд
неорганических соединений при температуре
200-600°С может взаимодействовать с полимерными
веществами, способствуя, с одной стороны, их
трансформации в углеграфитовые структуры, а с
другой, образованию летучих компонентов, что
приводит к газификации и образованию развитой
пористой структуры (активация). Наиболее часто
для твердофазной активации используют ZnCl2,
KOH, NH4Cl, фосфорную кислоту и ее соли. Эти
соединения можно назвать добавками активации
(ДА). Введение ДА в структуру волокон возможно
путем пропитки готовых полимерных волокон
растворами ДА и путем их введения в компаунды для
формования волокон.
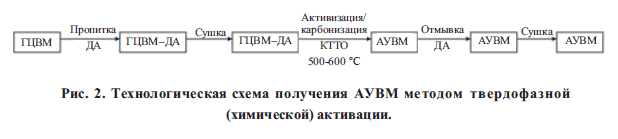
На рис.2 представлена возможная схема
получения химически активированных углеродных
волокон (УВ) с использованием готового
гидратцеллюлозного волокна (ГЦВ) или материала
(ГЦВМ). На рис.3 приведена схема получения АУ ВМ с
использованием компаундов для формования
волокон. В этом случае в качестве
углеродсодержащей основы (прекурсоров) могут
быть использованы растворы полиимидов,
фенольных смол, лигнина, полиакрилонитрила, пеки
и др.
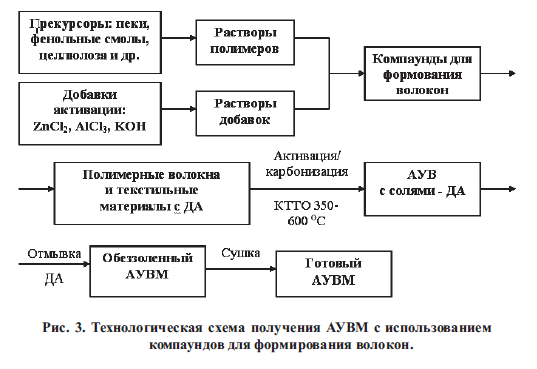
Использование твердофазной активации
позволяет совместить стадии активации и
карбонизации и соответственно получать АУВМ с
применением только одного вида оборудования -
печей карбонизации. Кроме того, так называемые
процессы газификации возможны уже при
температуре 200-300°С, и химически активированные
углеродные волокнистые материалы теоретически
могут быть получены в интервале температуры
350-550°С, когда прошла карбонизация, что
значительно снижает энергозатраты и
продолжительность модификации волокон-
прекурсоров. По-видимому, чем ниже температура
начала карбонизации волокон и образования
углеродных, трехмерно сшитых структур, тем при
более низкой температуре могут быть получены
пористые волокна-сорбенты. При снижении конечной
температуры термообработки (КТТО) увеличивается
выход углеродного волокна, что также
экономически выгодно (выход углеродного волокна
- это количество углеродного волокна в % (масс),
которое сохранилось после глубокой
термообработки, по сравнению с массой исходного
продукта).
Вместе с тем использование ДА в
большинстве случаев приводит к необходимости
отмывки АУВ от их остатков или продуктов их
взаимодействия с веществами основы АУВ. Возможно
ли получение химически активированных АУВ М по
способу, исключающему отмывку от ДА? Логично
предположить, что такой вариант возможен при
условии полного распада ДА в интервале
температур карбонизации/активации. При этом
должны быть соблюдены условия для сохранения
пористой структуры, образовавшейся в объеме
филаментов, т.е. не должен произойти ее коллапс.
Нами по данным работ [18-21] проведен
сравнительный анализ параметров активации и
свойств АУВ из полиакрилонитрила, полученных
активацией водяным паром, кислородом и с
использованием КОН. Установлено, что образцы,
активированные водяным паром, имеют
преимущественно мезопористую структуру;
образцы, активированные кислородом, являются
преимущественно ультрамикро- и
супермикропористыми. Химическая активация
позволяет получать микропористые волокна с
низким содержанием ме- зопор. Свойства АУВ,
полученных с использованием различных методов
активации, представлены в табл.1.
В работе [22] показана принципиальная
возможность получения высокоэффективных
сорбентов на основе фенольных смол методом
твердофазной активации с использованием КОН.
Сорбенты получали при нагреве смеси смолы и
активирующего агента в интервале температуры
500-600°С. Образцы имели удельную поверхность до 2300
м2/г и объем сорбционного пространства до
1.21 см3/г; при высокой степени активации
отмечено увеличение количества мезопор в
структуре материалов.
Оригинальный способ получения
бикомпонентных химически активированных
волокон разработан Экономи с сотр. [23]. Способ
основан на пропитке стеклянных волокнистых
материалов растворами различных полимеров,
содержащих химические активаторы, с последующей
химической активацией/карбонизацией
органической части материалов. В качестве
полимеров были использованы поливиниловый спирт
(ПВС), полиакрилонитрил (ПАН), целлюлоза,
фенольные смолы. Химическими активаторами
служили ZnCl2 и H3PO4.
К достоинствам разработанных
материалов следует отнести их прочность (за счет
стекловолокна) и низкую стоимость, которая, по
оценке авторов [23], не должна превышать 7-12 долл./кг,
что сопоставимо со стоимостью активированных
углей - 2-4 долл./кг. По-видимому, в качестве одного
из недостатков этого типа материалов можно
назвать их высокую плотность. По данным сайта http://economy.mse.uiuc.edu/research.htm,
выпуск таких материалов начат в
полупромышленном масштабе. Сорбционные
характеристики бикомпонентных АУВМ
представлены в табл.2.
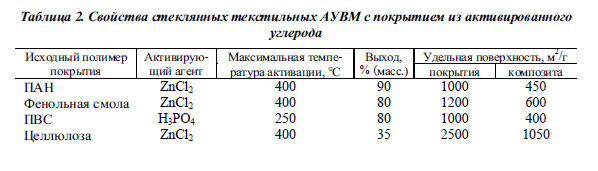
Приведенные выше сведения показывают,
что методом химической активации могут быть
получены АУВМ с высокими сорбционными
характеристиками из различных полимерных
прекурсоров. При этом в большинстве случаев
температура процессов активации/кар- бонизации
значительно ниже температуры активации и
карбонизации газофазных процессов.
В настоящей статье рассматриваются
результаты исследования твердофазной активации
гидратцеллюлозных (вискозных) волокнистых
материалов. В качестве активирующих агентов (ДА)
использовали ZnCl2, Na2PO4, , KOH.
Одновременно оценивали влияние ДА на выход
углеродных материалов в процессе термообработки.
Термообработке подвергали ленты из
гидратцеллюлозных кордных нитей,
импрегнированных растворами ДА различной
концентрации. Объектами сравнения служили ленты,
пропитанные кремнийорганической добавкой СИ-2, и
ленты без пропитки.
Результаты термогравиметрических
испытаний добавок (рис.4) показали, что хлорид
аммония, хлорид цинка и СИ-2 разлагаются
полностью при температуре 350, 800 и 500°С
соответственно. Наименее термостабилен хлорид
аммония, который начинает интенсивно
распадаться на NH3 и HCl при 200°С. Как показано
ранее [24], потеря массы сопровождается ярко
выраженным эндотермическим эффектом.
Кристаллогидрат динатрийфосфата
значительно теряет массу в интервале
температуры 80-180 °С, но его остаток после пиролиза
при 200°С стабилен даже при 800-900°С. Потеря массы
фосфата натрия, по-видимому, обусловлена
отщеплением воды, термостабильным остатком,
вероятнее всего, является тринатрийфосфат [25].
Кремнийорганическая добавка
термостабильна вплоть до 450°С. Прогрев при более
высокой температуре приводит к резкой потере
массы без заметных термических эффектов.
Хлорид цинка в интервале температуры
от 20 до 500°С постепенно теряет до 20% массы, в
интервале 500-650°С - еще 30% массы. Затем, при
повышении температуры на 50 град, теряется 40-45%
массы, при этом наблюдается отчетливый
эндотермический эффект, связанный с испарением
соли [25].
Исследования процессов
термодеструкции вискозных волокон, пропитанных
различными добавками, показали (рис.5), что
использование таких соединений как Na2HPO4,
NH4Cl и ZnCl2 приводит к значительному
увеличению выхода УВ по сравнению с выходом УВ
при получении без добавок. Выход УВ при добавке NH4Cl
составляет 3 8%, а в случае с ZnCl2 - 30%. Выход УВ
при карбонизации вискозных волокон без добавок
не превышает 8-10%. Небольшое увеличение выхода УВ,
на 10%, наблюдается также при проведении
карбонизации в присутствии добавки СИ-2.
Характеризуя выход УВ, следует
учитывать и тот факт, что добавки СИ-2, NH4Cl и
ZnCl2 при конечной температуре
термообработки (КТТО) 800°С удаляются из структуры
углеродных волокнистых материалов полностью.
Иная картина наблюдается при использовании в
качестве добавки Na2HPO4. Выход УВ (см.
рис.5) при КТТО 800°С (20%) нельзя считать истинным,
так как в УВ может содержаться до 50% остатков
термолиза добавки.
Таким образом, если по результатам
дериватографического исследования процесса
карбонизации ГЦВ, пропитанных Na2HPO4,
кажущийся выход (выход брутто) УВ составляет 20%,
то истинный выход (выход нетто) не превышает 10-12%.
Значения выхода нетто, рассчитанные по
данным дериватографических исследований, были
проверены путем оценки изменения массы
карбонизованных образцов после отмывки от
остатков добавок водой. Результаты
экспериментов для образцов, пропитанных
растворами добавок с различной концентрацией,
представлены в табл.3, там же приведены данные,
характеризующие прочность и пористость УВМ.
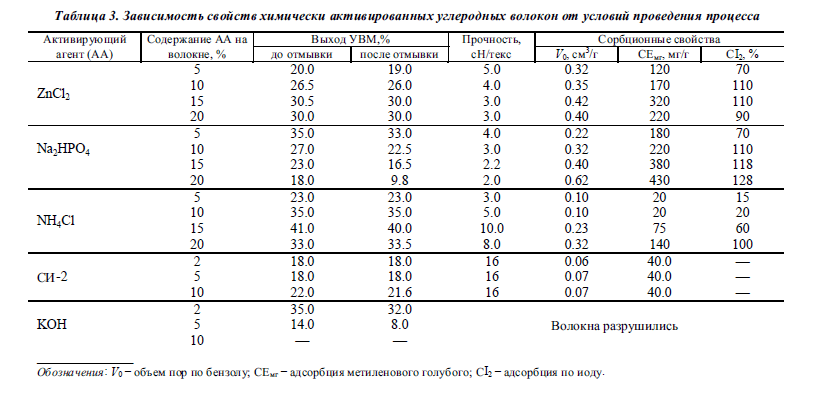
Использование в качестве ДА хлорида
цинка позволило получить АУВ с высокими
сорбционными характеристиками (V0 = 0.42
см3/г) и высоким выходом углеродных волокон
(30%). Оптимальным содержанием этой добавки в
структуре исходных волокон, по-видимому, можно
считать 15-18%.
Оптимальное содержание NH4Cl в
импрегнированных ГЦВ лежит в пределах 15-20%, что
позволит получать АУВ с общим объемом
сорбционного пространства до 0.30-0.32 см2/г и
неплохими прочностными характеристиками. При
использовании NH4Cl выход углеродных волокон
может достигать 40-41%.
Использование Na2HPO4
позволило получить АУВ с объемом сорбционного
пространства до 0.62 см3/г. Эта добавка, по-видимому,
может быть использована на практике, однако
активация/карбонизация проходит с низким
выходом АУВ. Вместе с тем уместно отметить, что
при активации паром карбонизованных волокон,
полученных с добавкой СИ-2, выход АУВ также не
превышает 8-10%. Тем не менее, такие АУВ остаются
конкурентоспособными [1].
Самая высокая прочность углеродных
волокон, 16 сН/текс, наблюдалась в случае
использования в качестве добавки СИ-2. Выход
составил 20-22%, однако объем сорбционного
пространства не превышал 0.19-0.20 см2/г.
Получить АУВ с использованием КОН не
удалось, что может быть связано с высокой
гидролитической активностью щелочи по отношению
к макромолекулам целлюлозы.
Представляло интерес изучить влияние
температуры термообработки на выход и свойства
АУВ. Эксперименты проводились с использованием в
качестве ДА хлорида цинка. Конечная температура
термообработки импрегнированных ГЦВ с
содержанием добавки 15-18% задавалась в пределах
350-550°С. Карбонизация/активация проводились, как и
в предыдущих экспериментах, в среде азота.
Основные результаты представлены в табл.4.
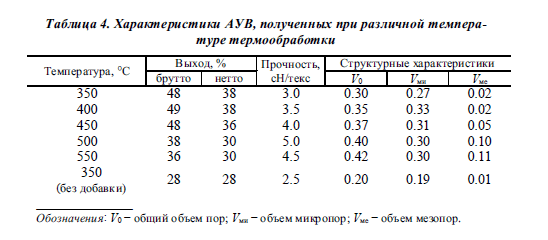
Анализируя полученные результаты,
можно констатировать, что снижение температуры
термообработки приводит к увеличению прочности
АУВМ и выхода готовых углеродных, в том числе
активированных, волокон.
При снижении КТТО объем сорбционного
пространства химически активированных АУВ
снижается до 0.40-0.42 см3/г при температуре
500-550°С, а при КТТО 350°С - до 0.30 см3/г, при этом
увеличивается доля микропор в сорбентах.
Касаясь механизмов порообразования в
объеме волокон при химической активации,
возможно предположить два основных вида физико-химических
процессов:
образование в структуре
карбонизующихся волокон микрокристаллов солей
ДА или продуктов их распада. Твердые
нанодисперсии после формирования углеродного
скелета могут быть экстрагированы из волокон,
что и формирует пористую структуру. Формирование
пористой структуры УВМ по этому механизму тем
вероятнее, чем ниже температура термообработки и
более термически устойчива ДА, чем менее
реакционноспособны по отношению к полимерным
молекулам продукты распада добавок;
формирование пористой структуры АУВ
в результате химического воздействия ДА или
продуктов их термораспада на полимеры волокон-прекурсоров.
Если при таком взаимодействии образуются
низкомолекулярные (смоляные) летучие продукты,
то порообразование происходит за счет их
возгонки при пиролизе.
Газификация и порообразование более
ярко выражены при увеличении количества добавки,
введенной в волокна-прекурсоры, и при повышении
температуры термообработки. К тому же повышение
КТТО зачастую приводит к распаду самих ДА, что
усиливает вероятность химического
взаимодействия как с полимерной основой волокна,
так и с углеродным скелетом карбонизующихся
волокон.
Показаны возможность и эффективность получения АУВ методом твердофазной (химической) активации волокон-прекурсоров различной природы
Изучены некоторые закономерности активации гидратцеллюлозных волокон с использованием добавок ZnCl2, NH4Cl или Na2HPO4
|